Why were you drawn to 9Wood?
The reason I was drawn to 9Wood was because I wanted to be a part of an organization that publicly posted its values and really lived by them, specifically improving the quality of life of each of the stakeholders in our organization. Each person here plays a key part. What we actually accomplish in a day matters.
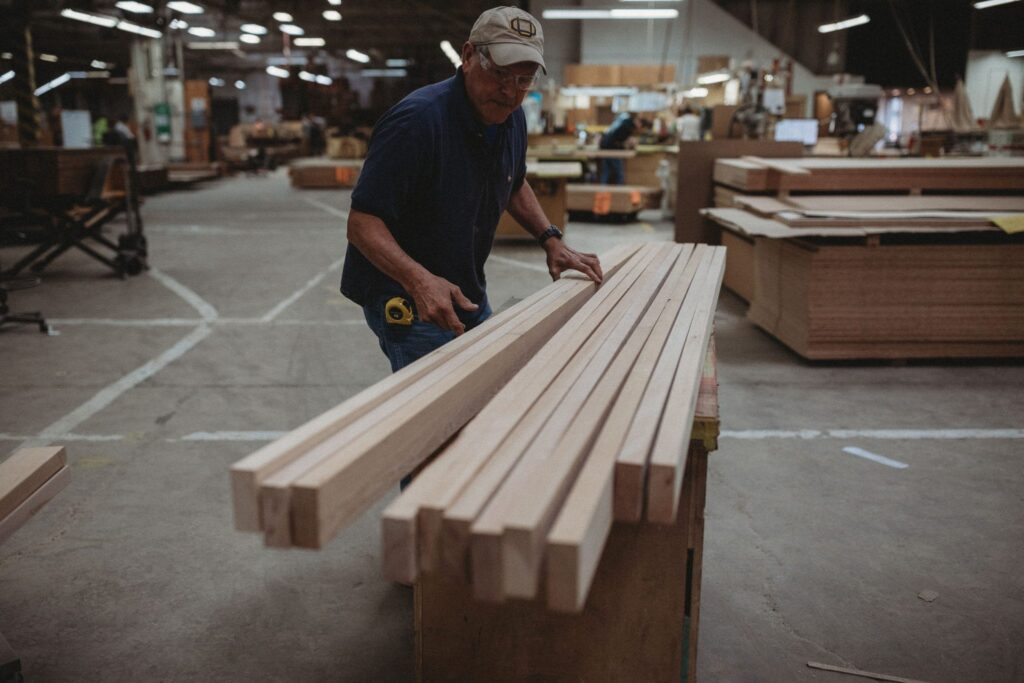
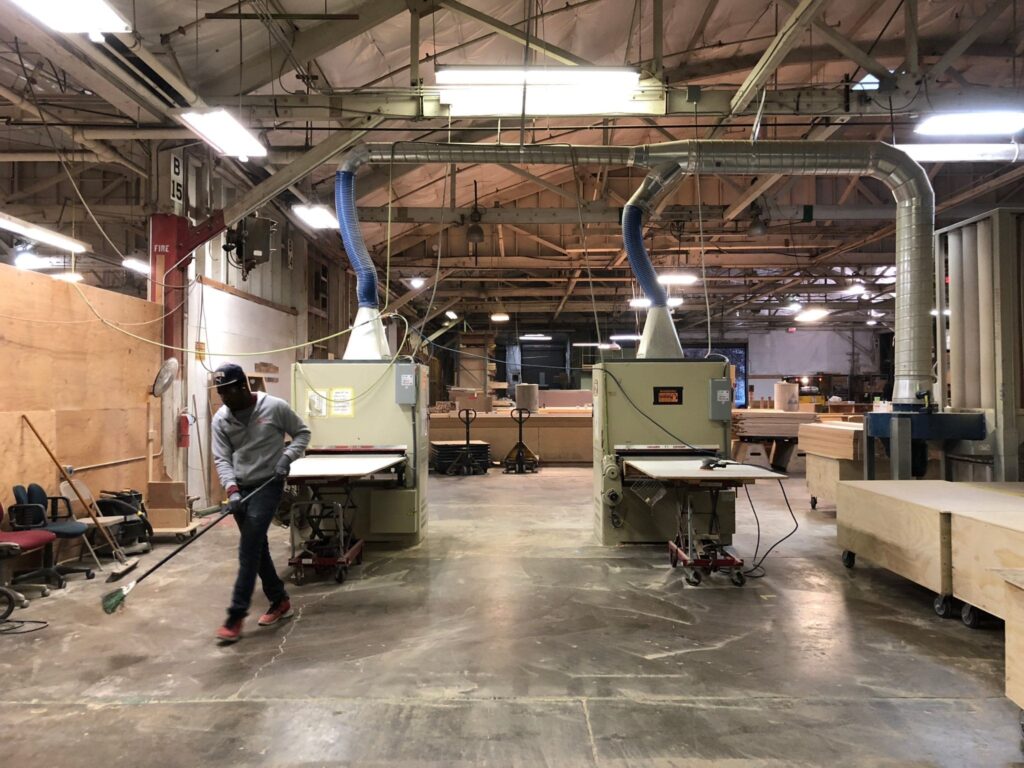
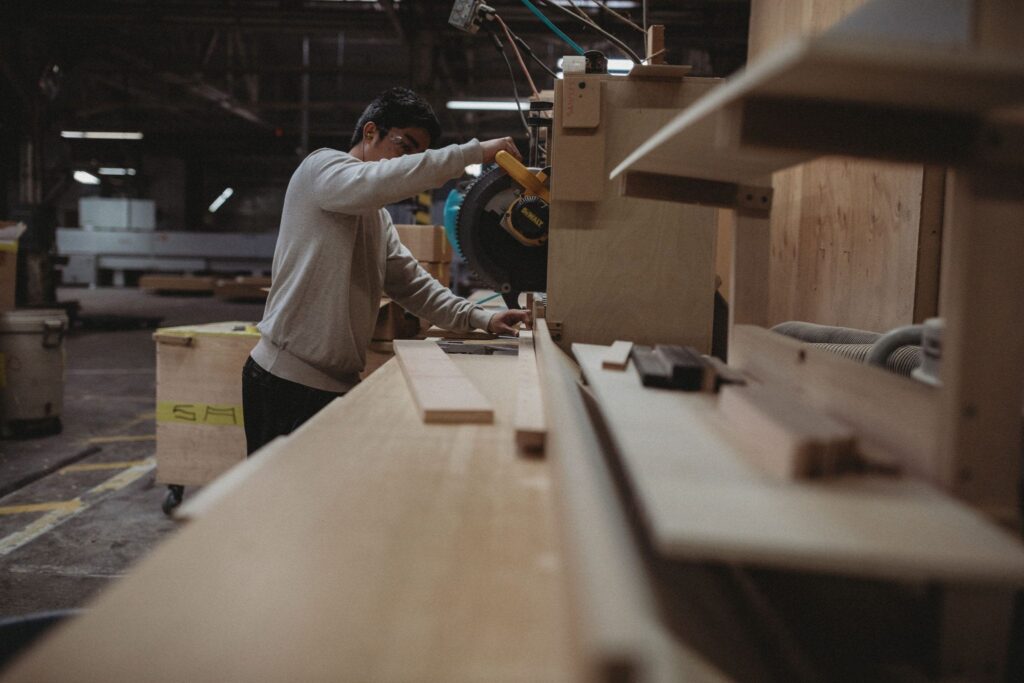
Since 9Wood is located within the raw material basket of wood products, there are a lot of people in the local area who have grown up or their careers have developed all within the wood industry. We have the benefit of drawing from a labor pool of people who have lots of different experiences that they bring to 9Wood, all related to wood, which helps us add value.
How does 9Wood train people?
Even though we benefit from the experience that each worker brings to 9Wood, we still have a very robust training program. With our TWI (Training Within Industry), we have standardized the work processes and we train each one of those skills individually for workers as they join the team. On-time performance takes improvement through people.
What are the most important metrics for production?
Our number one metric outside of safety here at 9Wood is our on-time metric. We have heard over and over from our customers that reliability is king. When we make a commitment to deliver a product at a certain time, we want to hit that as often as possible. A couple of years ago, we had an 85% on-time here at 9Wood, which some could consider ok, especially within this industry. Because of certain initiatives we have deployed over the last 2 years, we improved that on-time percentage to 96% last year.
What is 9Wood’s on-time performance?
9Wood’s on-time performance this year has been 97% and we’ll continue to improve that as we work. 2020 is definitely a challenging year, and we had a lot of wildfires here in Oregon that got really close to the plant and affected our employees very personally. Of course, there’s the COVID-19 Pandemic which creates a lot of variability in our schedule and in our labor force.
There are two specific things at 9Wood in production that allow us to be 97% on-time. One is the skill buffering that allows us to move skilled labor to where the work is. The other is our proprietary scheduling system that strategically buffers us against this variability.
Does 9Wood stock finished products?
We do not keep an inventory of finished products. Strategic buffers in our production process allow us to stage work in front of key resources. It also allows us to gain visibility of the processes that are not delivering on time, which allows us to focus on the improvements. Our scheduling system is decoupled in the middle of our value-added process from unloading the truck up to a certain point of value-added are scheduled separately from the rest of the plant.
We have an inventory of material that is already value-added. The materials we hold and buffer are not just for Fast>Track, although all the Fast>Track SKUs are supported by these buffers.
Who makes it work?
Behind all these processes that we’ve talked about – skill buffering, training initiatives, material buffering, we recognize behind all of that the thing that really makes 9Wood successful from an on-time performance and quality perspective are our valuable team members that we have in production and the rest of 9Wood. We partner with our employees to create value in their life, just like they create value in the 9Wood product for you.